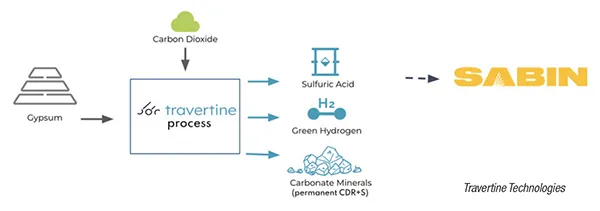
Transforming Waste: Groundbreaking Plant Upcycles Gypsum into Vital Chemicals
2024-12-01
Author: Benjamin
Overview of the Gypsum Upcycling Plant
In a revolutionary move for sustainable practices, a new demonstration plant is set to upcycle gypsum (calcium sulfate) at a metal-refining site. Gypsum, often seen as a challenging waste to manage, is now being transformed into valuable products through a cutting-edge process that integrates salt-splitting electrolysis, direct-air capture (DAC), and mineralization techniques.
Location and Technology Partnership
Located near Rochester, N.Y., this innovative facility, operated by Sabin Metal Corp., leverages advanced technology from Travertine Technologies, Inc., based in Boulder, Colorado. Owen Cadwalader, the company’s chief operating officer, explains that they will extract sulfuric acid, green hydrogen, and calcium carbonate from the legacy stockpile of mined gypsum accumulated before Sabin acquired the land.
Impact on Metal Recycling and Environmental Protection
But what does this mean for the future of metal recycling and environmental protection? The sulfuric acid generated from this process will play a crucial role in recovering precious metals, thereby enhancing the reclamation processes. Additionally, the creation of 'green' hydrogen opens the door to cleaner fuel options for the facility, further reducing carbon emissions.
Technology Breakdown
The technology utilized is both familiar and innovative, drawing inspiration from established industrial practices. The electrolyzer unit at the core of this process splits sulfate salts to produce sulfuric acid and caustic soda (NaOH), while also allowing for the generation of green hydrogen. The direct-air capture component then reacts caustic with ambient CO2 to generate sodium carbonate and release CO2-depleted air.
Benefits of Mineralization
The mineralization unit effectively processes waste gypsum, generating sulfate salts that are recycled back to the electrolyzer, along with a valuable byproduct: precipitated calcium carbonate. This calcium carbonate has the potential to serve as a permanent carbon sink, contributing positively to environmental efforts by potentially being utilized as a supplementary material in cement production.
Significance of the Project
This project marks a significant milestone as it stands to be the largest practical application of the Travertine Process to date, boasting a remarkable capacity of 125 tons per day of sulfuric acid. The facility is designed with a zero-liquid discharge principle, meaning that all inputs and outputs of the process are optimized to minimize waste.
Future Prospects
Stay tuned, as this innovative site could redefine waste management in metal refining and set a precedent for others to follow in the pursuit of greener industrial practices!