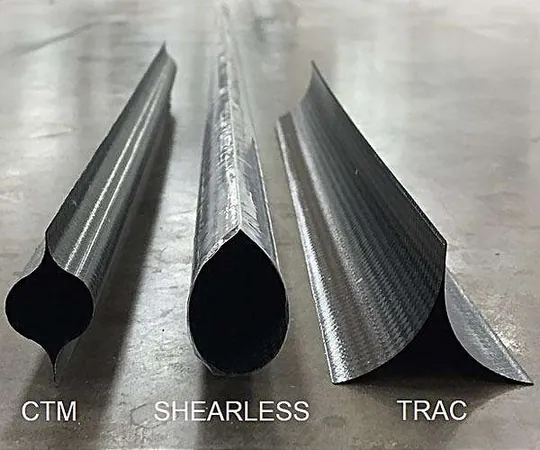
AnalySwift Revolutionizes Spacecraft Design with Groundbreaking Reconfiguration Technology
2024-11-20
Author: Yu
In an ambitious move to tackle the future of space missions, AnalySwift LLC, a company closely tied to Purdue University, has secured a Phase I STTR (Small Business Technology Transfer) contract worth $156,424 from NASA. This innovative initiative is set to transform the way spacecraft are designed and utilized during extended missions, especially for destinations such as the Moon and Mars.
Allan Wood, the president and CEO of AnalySwift, outlined the dual advancements this funding will support: the development of processes and hardware enabling the disassembly and reassembly of spacecraft components for secondary uses, and the creation of software for advanced multiphysics simulation that analyzes thermoplastic materials.
Dr. Kawai Kwok, an associate professor in Purdue's School of Aeronautics and Astronautics, is spearheading this project. He emphasized the significant logistical challenges posed by the current model, which relies on one-time-use components in highly demanding environments.
“Long-duration crewed missions will need infrastructures like trusses that can be built sustainably on other celestial surfaces without the need for heavy transport,” Wood stated. “Our project proposes a revolutionary approach to repurposing thermoplastic composite joints in space, allowing for the reconfiguration of structures instead of discarding them after a single use.”
Dr. Kwok added that with their method, spacecraft components can be swiftly transformed into entirely different shapes to meet varied mission requirements. For instance, a support truss for a lunar lander could be easily modified to become a vertical support structure for solar arrays.
Technological Innovations
One of the key deliverables from this contract will be the development of a composite heater layer that will be integral to the trusses and other supportive infrastructure. Embedded with nanostructured carbon fillers, this heater layer utilizes the same thermoplastic matrix as existing composite components and elevates the processing temperature for effective reconfiguration.
“Lightweight, conductive nanocarbon films will be encapsulated within semicrystalline thermoplastics like PEEK (polyether ether ketone),” explained Dr. Kwok. “Our method will use resistance welding, which enables us to reassemble the disassembled struts while using the same or additional heaters, ensuring our spacecraft's structures can be reused efficiently.”
In conjunction with these advancements, AnalySwift plans to enhance engineering tools for composite materials, enabling reliable multiphysics simulations. This new software module, dubbed Thermoplastic Composites Multiphysics, will model crucial processes such as the debonding and bonding at composite joint-strut interfaces.
Dr. Liang Zhang, a senior research scientist at AnalySwift, detailed that the simulation tool will track the necessary variables—force, pressure, and temperature—during these processes. By carefully solving these relationships, engineers can optimize the conditions required for robust reassembly, which could dramatically reduce the materials and logistical needs for space exploration.
Beyond Space Exploration
While the current focus is on space applications, the versatility of the new software could extend its impact to other domains. Wood pointed out that simulation capabilities could enhance the performance of high-grade thermoplastics in several industries including aerospace, automotive, and marine applications, as well as in the defense and electronics sectors.
With AnalySwift's trailblazing advancements, the future of space missions not only looks more sustainable but also holds the potential for groundbreaking innovations across multiple industries. Is this the dawn of a new era in spacecraft technology? Stay tuned as we follow AnalySwift's journey to redefine what is possible in space exploration.