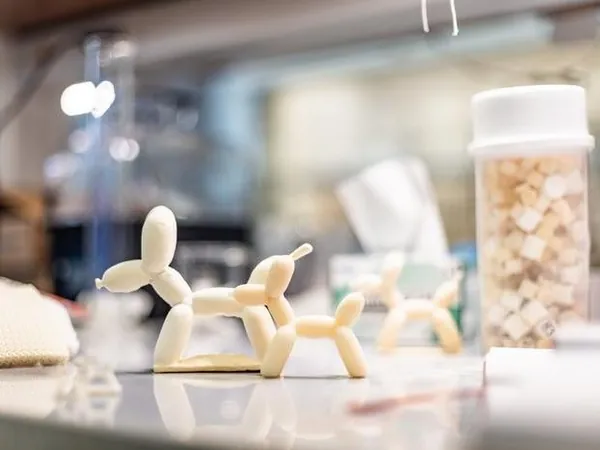
Breakthrough 3D-Printed Foam Could Revolutionize Manufacturing and Sustainability
2025-04-07
Author: Daniel
Introduction
In an exciting development from the University of Texas at Dallas, researchers have unveiled a groundbreaking 3D-printing formula that has the potential to transform the future of foam materials. Their research was highlighted in the March edition of RSC Applied Polymers, a respected journal published by the Royal Society of Chemistry, and focuses on creating a lightweight yet sturdy foam specifically designed for 3D printing—a method that remains underutilized in the commercial manufacturing sector.
The Research Team
Co-lead author and UT Dallas doctoral student, Rebecca Johnson, who aims to complete her PhD in chemistry this May, shared, "This is probably the longest project I’ve ever done." Over two years of dedicated work led the team to perfect a polymer formulation compatible with 3D printing technology, which is essential for creating custom products that cater to specific manufacturing needs.
Innovative Applications
The innovative foam can be used to form intricate shapes, with a balloon dog model serving as a playful proof-of-concept for their research. "Our goal was to tackle the limitations of current 3D printing methods for polymer foams," explained Dr. Ron Smaldone, an associate professor of chemistry and biochemistry involved in the study. He highlighted the foam’s tremendous potential for applications like insulation and shock absorption, critical for items ranging from motorcycle helmets to car bumpers.
Sustainability Features
One of the standout features of this new foam is its use of dynamic covalent chemistry. Unlike conventional thermoset foams, which undergo a chemical reaction during molding that renders them unrecyclable, the researchers have developed a foam that can repair itself when damaged. Although it cannot be completely melted and reshaped like traditional plastic, this capability significantly enhances its lifecycle and sustainability aspect, since it can minimize waste and landfilling.
Competitive Research Landscape
Dr. Smaldone acknowledged the competitive nature of this research, noting, "We’re certainly not the only ones trying to do this. The novel approach lies in utilizing dynamic chemistry to produce superior foam materials. Future studies will focus on fine-tuning the properties of this foam to meet diverse needs."
Future Directions and Impact
Ariel Tolfree, another co-lead author and chemistry doctoral student, is enthusiastic about the potential for advancing the sustainability of their product. Tolfree, who was mentored by Johnson, plans to explore how to make the foam more recyclable and assess its overall environmental impact.
Conclusion
The team’s whimsical choice of a balloon dog for their initial test model symbolizes the unexpected versatility of their foam. Tolfree quipped, "A balloon seems ordinary until it’s twisted into something new, almost defying expectations. Our foams are the same—unassuming at first, but once expanded and transformed, they become something remarkable."
With further research and exploration, the pioneers of this pioneering foam technology could soon herald a new era in manufacturing and sustainability, potentially impacting industries worldwide and fostering a greener future. The implications of their work may very well redefine the possibilities of materials science in the 21st century. Keep an eye on this revolutionary team as they continue to push boundaries!