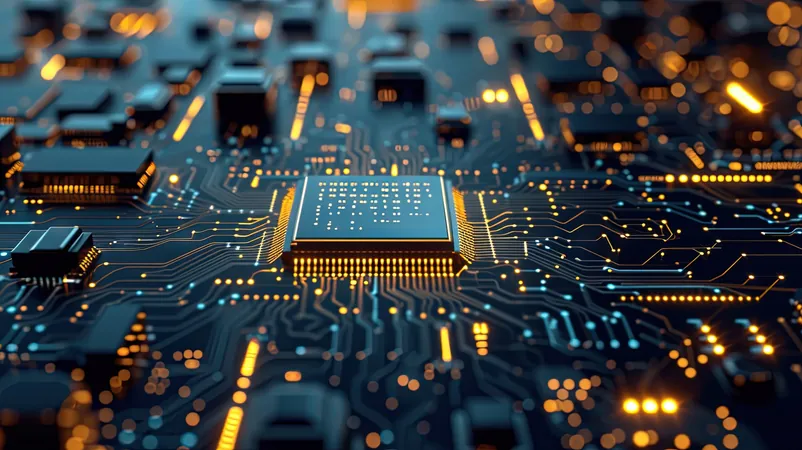
FOPLP Revolutionizes Advanced Semiconductor Packaging: The Future is Here!
2024-11-21
Author: Arjun
Introduction
Fan-Out Panel-Level Packaging (FOPLP) is breaking new ground in advanced semiconductor packaging, overcoming previous hurdles in manufacturability and yield. With the constant demand for higher integration densities and increased cost-efficiency in the tech industry, FOPLP is emerging as a formidable solution.
Historical Context
Historically favored in cost-sensitive sectors like consumer electronics and IoT devices, FOPLP's compact form and ability to integrate multiple dies have made it a staple, particularly for mature-node semiconductors. According to analysts from Yole Group, transitioning to panel-level formats can yield cost savings of 20% to 30% compared to traditional fan-out wafer-level packaging, which is especially beneficial for applications that require high throughput. This efficiency is largely due to the ability to process more dies simultaneously across larger usable panel areas.
Applications of FOPLP
In smartphones, FOPLP is frequently used for power management integrated circuits (ICs), RF modules, and audio amplifiers in mid-range to entry-level devices. Early wearables, such as fitness trackers, capitalized on FOPLP for their lightweight and thin designs without compromising on essential features. Beyond consumer electronics, its prevalence extends to IoT devices like smart home sensors and industrial monitors, where scalability and cost-efficiency are vital. The automotive industry has also embraced FOPLP in various applications, including infotainment systems and connectivity modules.
Manufacturing Innovations
As Doug Scott, senior vice president at Amkor Technology elaborated, FOPLP’s origin involved simplifying the manufacturing of lower-cost packages. Hence, large panel formats exceeding 600mm x 600mm have come into play. However, as the focus shifts towards creating complex, costly packages, there may be a need to shrink panel sizes to meet specific precision demands.
Benefits and Challenges
The benefits of FOPLP—cost efficiency, scalability, and simpler integration—have solidified its reputation as an efficient method for high-volume production, particularly for applications with less stringent performance requirements. In contrast, competing technologies like 2.5D interposers, while offering enhanced performance, often carry high costs and face technical issues limiting their widespread acceptance.
Cost Advantages
FOPLP presents potential cost advantages by enabling the use of larger panel formats to package more chips simultaneously. Chee-Ping Lee from Lam Research emphasized its flexibility in handling diverse materials and sizes, which can enhance productivity and yield while reducing costs. However, challenges such as initial equipment prices, limited supply chains, and processing yield due to the expansive formats could offset these savings for some applications.
Shift Toward Advanced Nodes
As the semiconductor industry shifts toward more advanced nodes, FOPLP is increasingly viewed as an optimal approach for applications in AI, 5G, and high-performance computing (HPC). The evolution of this technology is driven by a compelling need for high integration densities and cost-effective manufacturing solutions. However, hurdles remain in terms of material compatibility, improving yield, and addressing the lack of standardization in panel sizes, all of which must be tackled to allow broader adoption.
Industry Adoption
Notable companies like Samsung have made strides in utilizing FOPLP for advanced nodes—evidenced by the Exynos W920 processor that employs this technology alongside 5nm EUV processing. Reports indicate that Google is integrating FOPLP for its Tensor G4 chips, while tech giants AMD and NVIDIA are partnering with TSMC and other OSAT providers to implement it in their upcoming models, especially for complex AI GPUs and multi-die arrangements.
Looking Ahead
Despite the challenges that still loom over the FOPLP landscape—particularly concerning yield consistency and standard panel sizes—industry experts remain optimistic. TSMC is already making moves toward developing a 515mm x 510mm rectangular substrate that could vastly increase usable area compared to traditional 12-inch round wafers. Nevertheless, TSMC’s CEO, Che-Chia Wei, warned that achieving maturity in panel-level fan-out technology may still be a few years away.
Investment in Innovation
The transition to FOPLP demands significant investment not only in new materials and processes but also in advanced equipment geared for larger panel manufacturing. Controlling warpage and ensuring consistent material quality across large panels is critical for reliable interconnects in high-density designs.
Standardization Efforts
The introduction of SEMI’s 3D20 standards aims to standardize panel characteristics and facilitate equipment compatibility, but widespread adoption is still lagging. Currently, varying dimensions from 400mm x 500mm to 650mm x 650mm complicate the manufacturing landscape, necessitating custom solutions that drive up costs.
Conclusion
Looking to the future, FOPLP is on the verge of becoming a cornerstone in the advanced semiconductor packaging arena, especially as the market moves towards chiplet designs that offer cost and performance benefits in multi-die applications. With advancements in materials, processes, and collaborative frameworks within the industry, FOPLP not only aims to bridge the gap between high performance and mass manufacturability but also promises to transform the semiconductor landscape for years to come.
As we continue to witness the rising tide of technology, FOPLP stands at the forefront of advanced packaging solutions, making now the perfect time to pay attention to this evolving technology!