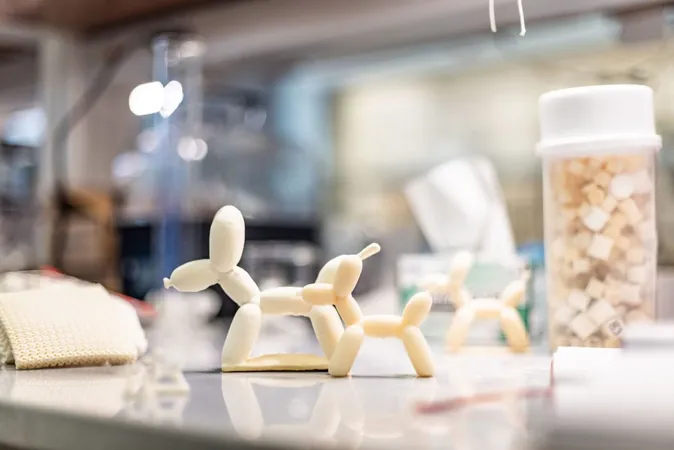
Revolutionary 3D-Printed Foam Could Change the Manufacturing Game
2025-04-02
Author: Wei Ling
Foam is more than just a cushion for our seats or a mere insulator in our homes; it permeates various aspects of our daily lives, often unnoticed. Now, researchers at The University of Texas at Dallas have developed a groundbreaking 3D-printed foam that promises to be both more durable and recyclable than the traditional polymer foams we commonly use. This could herald a new age in manufacturing and sustainability.
Published in *RSC Applied Polymers*, the research centers on creating a foam that is not only sturdy but also lightweight and suitable for 3D printing—a technique that remains underutilized in mainstream manufacturing, according to doctoral student and co-lead author Rebecca Johnson. Completing her Ph.D. in chemistry this May, Johnson shared that the project has spanned over two years, filled with challenges as the team fine-tuned the polymer formula for compatibility with their 3D printer.
The 3D-printing process empowered the researchers to craft intricate designs, including a playful balloon dog, showcasing the foam's bespoke capabilities. In addition, a YouTube video was released that captures their innovative work, providing a visual testament to their achievements.
“3D printing presents immense potential by overcoming limitations that traditional polymer foams face,” stated Dr. Ron Smaldone, an associate professor in the School of Natural Sciences and Mathematics and the study's lead author. He pointed out that possible applications range from insulation and shock absorption to protective gear like motorcycle helmets, football pads, car bumpers, and even military armor. The technology paves the way for complex structures, enabling flexibility and versatility in design.
Another significant hurdle the researchers tackled was ensuring their 3D-printed foam maintained consistent quality with minimal defects. Most commercial foam is thermoset and irreversibly locks into a shape when molded, rendering it non-recyclable and contributing to landfill waste. In contrast, UT Dallas researchers devised a robust foam using a unique approach involving reversible bonds—dynamic covalent chemistry. This innovation means the foam can self-repair when damaged, offering a longer lifespan while being more adaptable for various uses.
“We’re not the sole players in this field, but our key contribution is the application of dynamic chemistry for creating advanced foam materials. The next step is tuning these properties to meet diverse industrial needs,” Dr. Smaldone noted.
Ariel Tolfree, co-lead author and chemistry doctoral student, worked alongside Johnson and plans to further investigate ways to enhance the foam’s recyclability and assess its sustainability. They chose the whimsical balloon dog as part of their project, symbolizing the foam's potential. "At first glance, a balloon appears simple until it’s molded into something extraordinary. Our foams share that essence—they may seem ordinary but can transform into remarkable forms when utilized,” Tolfree explained.
As the research continues to evolve, this pioneering project could set the stage for a revolution in how we think about and utilize foam in modern manufacturing. With an eye towards sustainability and innovation, the future of foam may soon be on the verge of a significant transformation. Stay tuned, as this could redefine various industries and contribute to a more eco-friendly world!