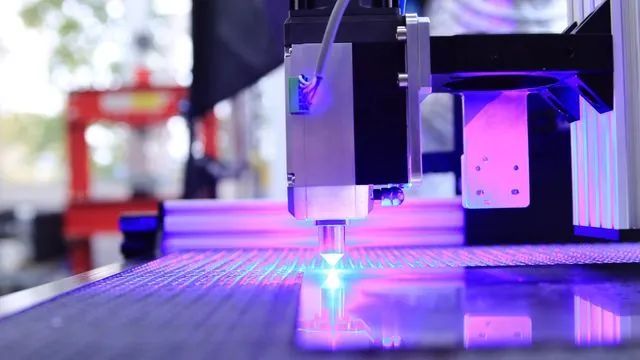
Revolutionary 3D Printing Technique Creates Stretchable, Flexible, and Recyclable Plastics!
2024-12-16
Author: Jia
Introduction
In a groundbreaking advancement set to change the materials science landscape, engineers from Princeton University have unveiled a highly scalable 3D printing technique that produces soft plastics remarkably rich in properties—stretchability, flexibility, and recyclability—all at an affordable price point.
Research Details
Published in the esteemed journal Advanced Functional Materials, the research led by chemical and biological engineering professor Emily Davidson introduces a way to manufacture soft 3D-printed structures using a commonly available class of polymers known as thermoplastic elastomers. These innovative materials allow engineers to manipulate the plastic's stiffness and elasticity during the printing process. The result? Devices that can flex effortlessly in one direction while maintaining rigidity in another!
Microscopic Architecture
The secret sauce behind these super-materials lies within their unique microscopic architecture. By utilizing a special type of block copolymer that forms stiff cylindrical structures measuring just 5-7 nanometers thick (to put that into perspective, a human hair is about 90,000 nanometers thick), the researchers have created an elastic polymer matrix that showcases a mix of both rigidity and stretchiness. By carefully orienting these nanoscale components during 3D printing, it is possible to design materials that exhibit variable flexibility and strength based on their location within an object.
Cost-Effectiveness and Manufacturing Process
The journey to this breakthrough began with selecting the right kind of polymer. The team chose thermoplastic elastomers—block copolymers that can be reshaped and cooled into elastic materials—which are far more cost-effective than traditional alternatives, costing merely one cent per gram compared to other materials priced upwards of $2.50 per gram. Moreover, these elastomers can be printed using standard commercial 3D printers, dramatically streamlining the manufacturing process.
Self-Healing Properties
One of the standout features of this technique is the role of thermal annealing, a heating and cooling process that not only enhances the mechanical properties post-printing but also gives the printed objects the ability to heal themselves from damage. Graduate student Alice Fergerson, who is the lead author of the study, emphasizes, “Thermal annealing drastically improves properties and allows for high reusability, meaning we can repair items through this technique.”
Integration of Functional Additives
The researchers have successfully integrated functional additives into their thermoplastic elastomers without compromising control over the material's attributes. They even added a special organic molecule that causes the plastic to glow red under ultraviolet light—showcasing how versatile this technique can be. Their capacity to print intricate multi-layered designs, from a tiny plastic vase to printed text spelling “PRINCETON” in sharp turns, is nothing short of impressive.
Future Directions
As promising as these results are, the researchers are not stopping here. They plan to extend their focus into new 3D-printable architectures suitable for applications in wearable electronics and various biomedical devices.
Conclusion
This pioneering work has the potential to reshape industries by offering affordable, customizable materials that can adapt to complex demands in the modern world, proving that the future of plastics is not only bright but also flexible and sustainable! Stay tuned as this research unfolds, paving the way for innovations that could dramatically impact how we design and use materials in everyday life.