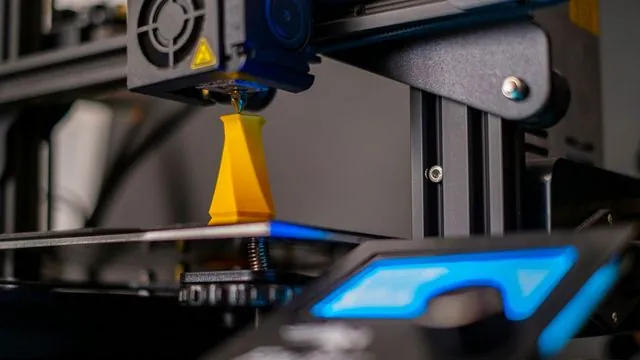
Revolutionary Breakthrough in 3D Printing: Engineers Develop Method to Eliminate Metal Part Defects!
2024-11-25
Author: Arjun
Introduction
In a groundbreaking advancement for 3D printing technology, engineers from the University of Wisconsin-Madison have discovered a method to simultaneously address three major defects in metal parts produced through the highly regarded laser powder bed fusion technique. Under the leadership of Lianyi Chen, an associate professor of mechanical engineering, the team’s exciting findings were published in the November 16, 2024 edition of the International Journal of Machine Tools and Manufacture.
Innovative Approach
Traditionally, efforts to reduce defects in 3D printing have focused on one issue at a time, often requiring separate methods to tackle the remaining problems. However, this innovative approach launched by Chen's team has the potential to mitigate all three defects—pores, rough surfaces, and large spatters—simultaneously! This not only leads to better quality metal parts but also significantly speeds up the manufacturing process without sacrificing quality.
Industry Implications
The implications of this research extend far beyond the lab. As industries including aerospace, medical, and energy continue to adopt additive manufacturing to create complex metal parts that conventional methods struggle to produce, the challenge of defects remains a significant barrier. Defects such as voids and roughness can severely compromise reliability, particularly in critical applications where failure is not an option.
Technical Innovations
The team’s approach utilizes a specialized ring-shaped laser beam— a deviation from the standard Gaussian beam—provided by the leading laser company nLight. This key innovation plays a critical role in the reduction of defects, allowing for deeper drilling into the material without introducing instability during the printing process. This method also paves the way for producing thicker layers, thus enhancing productivity.
Research Methodology
To understand how materials behaved during the printing process, the researchers conducted in-situ experiments at the Advanced Photon Source, a prestigious synchrotron X-ray facility at Argonne National Laboratory. By combining high-speed synchrotron X-ray imaging with theoretical analysis and numerical simulations, the team revealed mechanisms that reduce instabilities in the laser powder bed fusion process.
Future Prospects
Jiandong Yuan, a PhD student in Chen’s group and lead author of the study, emphasized that the insights gained from understanding these mechanisms allowed for rapid identification of processing conditions that yield high-quality 3D-printed metal parts.
With the potential for improved quality and productivity, this breakthrough could accelerate the industry-wide adoption of laser powder bed fusion technology, ultimately revolutionizing the manufacturing of metal parts. The future of 3D printing may be brighter than ever, setting a new standard for reliability in critical applications.
Conclusion
Stay tuned for more developments in this exciting field as we continue to follow how these innovations could reshape the landscape of manufacturing!