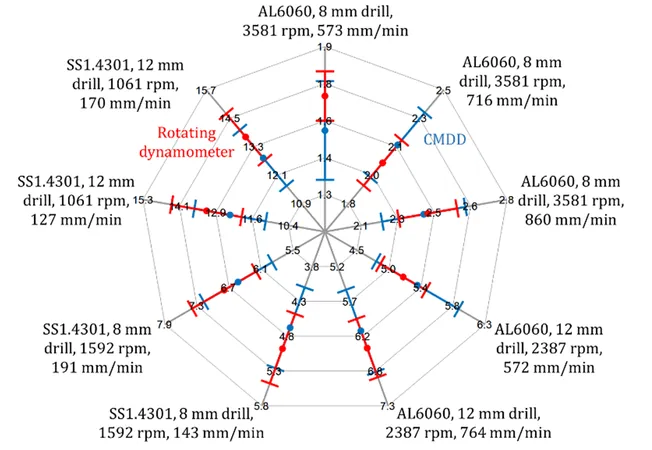
Revolutionizing Aerospace Manufacturing: The Game-Changing Role of Torque and Thrust Force Measurements in Smart Drilling Operations!
2024-12-23
Author: Wei Ling
Introduction
In an era where digital technologies are transforming manufacturing industries, low-cost and high-accuracy sensors have emerged as essential tools for enhancing productivity and efficiency. Features like torque and thrust force measurements are paving the way for smart manufacturing across critical sectors, including automotive, medical, aerospace, and agriculture. In aerospace specifically, reducing both time and cost during the drilling process is vital. By employing in-process measurements of torque and thrust force, manufacturers can assess tool wear in real-time and schedule timely tool changes, which is crucial given the millions of holes needed for assembling complex aerospace structures, such as riveted and bolted joints.
The Constrained-Motion Drilling Dynamometer (CMDD)
The development of a constrained-motion drilling dynamometer (CMDD) stands out as a brilliant innovation in this regard. This device, capable of measuring drilling torque and thrust force, operates without the burden of high costs or intricate setups. The CMDD employs a flexure-based design, where the drilling torque is determined by the rotational displacement of the workpiece mounting stage, while thrust force is calculated from the translational displacement of the platform.
Design and Functionality
The unique design incorporates ten flexure elements, known as "spokes," which allow the mounting stage to rotate around a vertical axis. Additionally, the platform's vertical translation is supported by four flexure elements. Hall effect sensors, known for their precision, play an instrumental role in measuring the displacements, which are then used to compute the required torque and thrust values.
The CMDD's structural platform is fabricated from durable 6061-T6 aluminum. Its performance characteristics, including rotational stiffness and vertical displacement capabilities, are intricately linked to the design parameters such as spoke length, width, and thickness. This interplay between design elements reveals how significant adjustments can lead to enhanced performance metrics, which can help manufacturers optimize their drilling processes even further.
Visualization and Testing
Contour plots were generated during testing to visualize the relationship between flexure element dimensions and stiffness values, aiding engineers in making better design choices.
Utilizing cutting-edge Hall effect sensors, the CMDD showcases how magnetic fields can precisely detect rotational and translational movements. Implementing a dual magnet configuration ensures linearity in readings, with a performance range that is critical for accurate data.
Validation and Results
To validate the robustness of the CMDD, rigorous drilling tests were conducted, comparing its results to those from the established Kistler 9170A1312 rotating dynamometer. The testing involved various materials, including 6060 aluminum and DIN EN 1.4301 stainless steel, while employing TiAlN coated drills to enhance effectiveness. The experiments aimed to ensure the process was not only efficient but repeatable, a crucial aspect in the aerospace sector where precision is non-negotiable.
Results revealed an impressive correlation between the CMDD readings and those of the commercial dynamometer, with discrepancies in torque and thrust force measurements remaining within an astonishing 8.2% and 7.9%, respectively.
Conclusion
The implications of these advancements in smart drilling operations are significant. As manufacturing industries, especially aerospace, continue to seek efficiency and cost reduction, tools like the CMDD stand poised to revolutionize the way structural assemblies are executed. This innovation not only represents a technological leap but also underscores a broader trend towards smart manufacturing—a future where precision and efficiency go hand in hand to meet the skyrocketing demands of modern production.
Stay ahead of the curve—discover how these innovations are set to reshape industries!