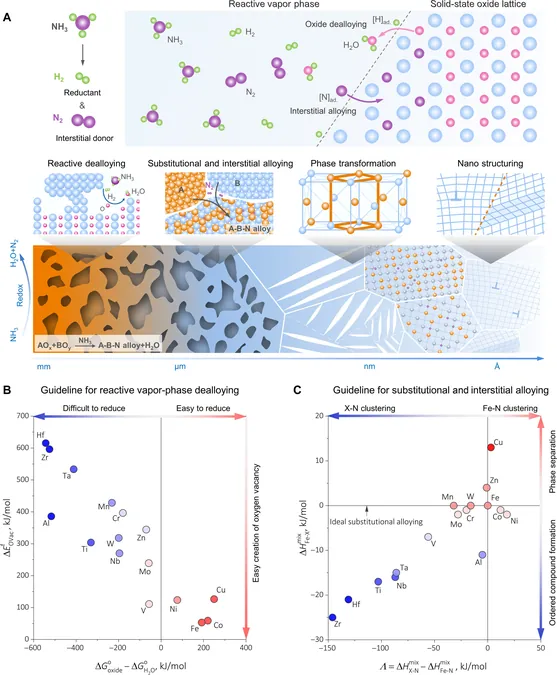
Revolutionizing Alloy Production: How Scientists Battled Corrosion to Create Lightweight Materials!
2024-12-18
Author: Yu
Introduction
In a remarkable breakthrough, researchers at the Max Planck Institute for Sustainable Materials (MPI-SusMat) have discovered a game-changing technique that transforms the destructive process of dealloying into an innovative method for producing lightweight, high-strength alloys. Traditionally viewed as corrosive, dealloying is now being repurposed in a sustainable, energy-efficient manner that could reshape the future of materials science.
Research Findings
Their ground-breaking findings, published in Science Advances, present a new approach that combines dealloying with alloying in a single process. By employing reactive gases like ammonia, the researchers are able to effectively remove oxygen from metal lattices while infusing them with nitrogen, resulting in nano-porous martensitic alloys. These materials may have a wide array of applications, from creating lightweight structural components to designing advanced functional materials, including potential alternatives to rare-earth magnets.
The Basics of Alloying and Dealloying
For centuries, alloying—mixing different metals and elements—has been foundational to metallurgy, allowing scientists to create materials with specific, desired properties. Meanwhile, dealloying has often been linked to deterioration and weakening of structures as it selectively leeches away certain elements. However, the MPI-SusMat team posed an intriguing question: Could dealloying be harnessed to generate beneficial microstructures instead?
Methodology and Process
Dr. Shaolou Wei, a Humboldt research fellow at MPI-SusMat and the publication's first author, describes their innovative vision: “Our goal was to remove oxygen from the lattice and control its porosity by creating and aggregating oxygen vacancies. This opens exciting pathways for the design of lightweight, high-strength materials.”
Central to their revolutionary technique is the use of reactive vapor-phase dealloying—a process where a reactive gas atmosphere 'attracts' oxygen atoms from the lattice, effectively extracting them. This atmosphere, rich in ammonia, plays a dual role: it not only reduces the lattice’s oxygen levels but also supplies interstitial nitrogen, enhancing the material's structural integrity.
"We're assigning specific roles to the atoms from both reaction partners, which is truly the key innovation in our approach,” says Professor Dierk Raabe, managing director of MPI-SusMat and corresponding author for the study.
Integrative Metallurgical Processes
The researchers ingeniously integrated four pivotal metallurgical processes into a single reactor step: 1. **Oxide Dealloying:** Eliminating oxygen to create porosity while using hydrogen to reduce metal ores. 2. **Substitutional Alloying:** Facilitating diffusion between metallic elements post oxygen removal. 3. **Interstitial Alloying:** Importing nitrogen into the lattice from the vapor phase. 4. **Phase Transformation:** Activating martensitic transformations for nano-structured enhancement.
Sustainability and Feasibility
This synthesis methodology not only streamlines production but also embraces sustainability by utilizing oxides and reactive gases like ammonia, as well as potentially taking advantage of industrial waste emissions. Because hydrogen is used as a reducing agent, the entire process remains CO2-free, producing only water as a byproduct. The feasibility of applying this technique to metals such as iron, nickel, cobalt, and copper has been confirmed through thermodynamic modeling.
Potential Applications
The nano-structured porous martensitic alloys resulting from this process are both lighter and stronger, attributed to precise control over the microstructure at multiple scales. This contrasts sharply with traditional methods that necessitate time-consuming and energy-intensive procedures to achieve similar porosity levels.
Potential applications are vast—ranging from lightweight structural components to high-performance iron-nitride-based hard magnetic alloys that could outperform rare-earth counterparts.
Future Aspirations
Looking to the future, the researchers aspire to extend this novel approach by experimenting with impure industrial oxides and alternative reactive gases. This could significantly decrease dependency on rare-earth materials and high-purity sources, aligning perfectly with global sustainability targets.
Conclusion
Thanks to the MPI-SusMat team, we are witnessing an exciting new era of alloy design that marries sustainability with innovative engineering. Their strategy of rethinking conventional processes not only paves the way for transformative advancements in materials science but may also lead the charge towards a greener future! Don’t miss out on what could be a revolutionary shift in manufacturing—stay tuned for updates on this groundbreaking research!