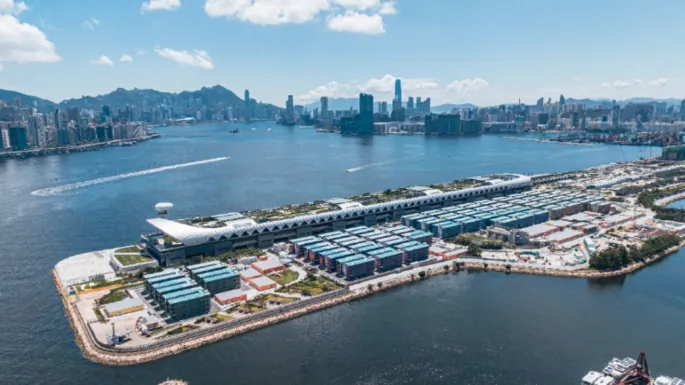
The Race to Cut Carbon in Hong Kong: Modular vs. Conventional Construction Unveiled
2024-10-09
Author: Ting
Introduction
As the world grapples with climate change, the urgency of reducing greenhouse gas emissions has never been clearer. The Paris Agreement of 2015, where 197 countries committed to limiting global warming to 2°C, catalyzed actions around the globe. Notably, the Intergovernmental Panel on Climate Change (IPCC) has underscored that to avert catastrophic climate outcomes, we must strive to limit warming to 1.5°C and cut greenhouse gas emissions by half by 2030, ultimately reaching net zero by 2050. Hong Kong is not exempt from this call to action; the local government has declared its ambitions to achieve carbon neutrality by or before 2050, setting interim goals of halving carbon emissions by 2035.
In this context, the construction sector stands at a critical junction. As one of the largest contributors to carbon emissions globally—accounting for nearly one-third of energy consumption and carbon output—transforming construction practices in places like Hong Kong is vital for its carbon neutrality goals. The construction industry is not only a significant economic driver, adding over HK$121.8 billion to the local GDP in 2022, but is responsible for approximately 90% of the city's electricity consumption and around 60% of its carbon emissions.
To evaluate the environmental impact of construction, Life Cycle Assessment (LCA) is frequently employed. In this study, we are narrowing our focus on embodied carbon—carbon emissions associated with materials production, transport, and construction—along with operational carbon, which emerges from energy usage during the building's lifecycle. Though operational carbon has typically dominated total building emissions (comprising 70% to 98% compared to just 2% to 26% from embodied carbon), advances in energy-efficient technologies and sustainable materials are redefining this balance.
What’s Happening in Modular Construction?
Modular Integrated Construction (MiC), which entails factory-made housing units, has gained traction in Hong Kong as a remedy for labor shortages and inefficiencies in traditional methods. With the mounting pressure to meet carbon reduction targets, the potential for MiC to slash embodied carbon gains significant attention. Recent studies have shown promise: precast concrete alone can produce 12.2% less carbon emissions compared to traditional cast-in-situ methods, while semi-prefabricated construction techniques can mitigate GHG emissions by up to 13.62%.
Yet, the literature presents gaps that could undermine effective decision-making. Most studies have been theoretical, lacking real-world applications and data specific to densely populated areas like Hong Kong where MiC implementation is still nascent. Comparative assessments of MiC against conventional techniques using the same design parameters are limited, thus hindering broader adoption and systemic improvements.
The Spotlight on the Kai Tak Community Isolation Facility
Addressing these gaps is crucial; hence, our analysis zeros in on the Kai Tak Community Isolation Facility (CIF), completed in August 2022, which exemplifies MiC in action. Spanning over 110,000 square meters with 2,700 units offering more than 6,000 beds, Kai Tak CIF serves as a compelling case study for examining the embodied carbon implications of MiC. Utilizing real project data provided by China State Construction (HK) Limited, this analysis conducts a side-by-side assessment with a conventional construction alternative designed for direct comparison.
Research Insights: A Carbon Showdown
The findings reveal a stark contrast in embodied carbon emissions: while Kai Tak CIF constructed via MiC emitted 46,024 tons of CO2 equivalent, conventional methods would have yielded approximately 58,005 tons—highlighting a significant reduction of about 20.7% emissions with MiC. In terms of construction materials alone, the MiC approach realized 6.1% lower carbon emissions, primarily due to its reliance on structural steel and precise material usage, which resulted in lighter structures.
However, the journey to sustainability is riddled with challenges in an urban environment like Hong Kong. Transportation constraints and the need for dense support structures can restrict the design flexibility of MiC. Nevertheless, essential opportunities for innovation remain. For instance, employing cargo ships for transportation could alleviate current limitations and enhance material efficiency.
The emphatic reductions in the operational emissions associated with construction are noteworthy as well. The MiC method led to just under 5,707 tons of operational emissions, a formidable decrease of 58.1% compared to the conventional counterpart, proving its case not just for carbon savings but also for reduced community disruptions and noise pollution.
Conclusion: A Path Forward
While the environmental benefits of MiC are clear, further research into fully modular constructions and case-specific factors continues to be necessary to ensure the comprehensive understanding of its potential within high-density urban settings. Moving forward, both policymakers and industry leaders must embrace these findings and commit to the adoption of innovative construction practices. Thus, the construction landscape in Hong Kong could become a model for balancing development and environmental responsibility in the coming age of climate action.
By understanding and leveraging these insights, Hong Kong can not only meet its carbon neutrality goals but also set an example for other high-density cities around the world.