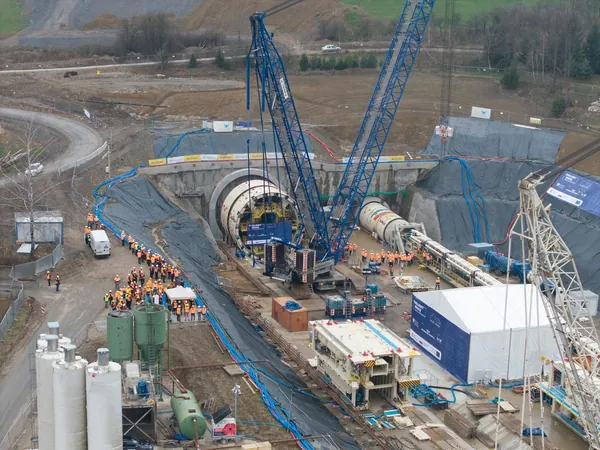
Tajfuny, rebelianci i gigantyczne wyzwanie czasowe. Kulisy budowy najdłuższego tunelu kolejowego w Polsce
2025-04-06
Autor: Magdalena
Na koniec marca konsorcjum Budimex i Gülermak ruszyło z budową najdłuższego tunelu kolejowego w Polsce, który ma długość 3,75 km i łączy miejscowości Męcina-Mordarka. To kluczowy element modernizacji linii nr 104, łączącej Limanową z Klęczanami, a kwota inwestycji wynosi 1,9 miliarda złotych.
Budowa tego tunelu odbywa się w kontekście pilnych ram czasowych, gdyż projekt jest finansowany z Krajowego Planu Odbudowy (KPO) w ramach wsparcia Unii Europejskiej dla gospodarek dotkniętych pandemią. Niestety, przez spory dotyczące praworządności w Polsce, fundusze były przez długi czas zamrożone, co spowodowało, że wykonawcy muszą teraz działać szybko, by dotrzymać wyznaczonego terminu zakończenia prac do 31 sierpnia 2026 roku.
Z interesującym twistem, maszyny używane do budowy tunelu zostały wyprodukowane w Chinach przez firmę China Railway Construction Heavy Industry Corporation Limited. Główne narzędzie, maszyna TBM (Tunnel Boring Machine) o nazwie „Jadwiga”, ma średnicę tarczy prawie 11 m, podczas gdy mniejsza, „Kinga”, wszechstronna maszyna o średnicy około 4,8 m, będzie pracować nad tunelem ewakuacyjnym.
Warto dodać, że problem z transportem tych maszyn nasiliły napięcia międzynarodowe i warunki pogodowe, w tym tajfuny, które opóźniły wypłatę maszyn z portów w Chinach. Transport morski został wybrany jako najszybsza opcja, ale podlegał on zawirowaniom związanym z atakami ze strony rebeliantów w Jemenie, co wprowadza dodatkowe ryzyko wręczania maszyn do Polski.
Dodatkowo, podpisać warto, że chiński producent nie jest nowicjuszem na rynku. W swoim portfelu ma m.in. projekt TBM, który wykopał ponad 39 km tunelu w Chinach, co czyni ich jednym z liderów w tej branży. Pomimo tego, że do transportu wybrano porty w Gdyni i Gdańsku z uwagi na ograniczenia infrastruktury, to zrealizowanie całego procesu dostawy wykazało się niemałym wyzwaniem.
Budowa tunelu odbywa się w trudnych warunkach geologicznych, a głębokość jego drążenia wynosi 120 metrów. Co piątą metrze napotykany jest inny rodzaj gruntu, a presja wodna stanowi dodatkowe zagrożenie. Praca maszyn TBM zaczyna się od drążenia, a następnie układania prefabrykowanych pierścieni z żelbetu, a każdy cykl wymaga precyzyjnego działania i zaawansowanej technologii na każdym etapie działania. Planowane tempo drążenia to od 8 do 12 metrów na dobę oraz praca na trzy zmiany, co oznacza intensywny proces budowy.
Całość projektu, który obejmuje nie tylko tunnel ale także modernizację i elektryfikację linii kolejowej oraz budowę nowych odcinków, ma realnie wpłynąć na poprawę komunikacji w Małopolsce, skracając czas podróży między Krakowem a Nowym Sączem do jedynie godziny.
Zainwestowane środki oraz nowoczesna technologia mają zatem potencjał, aby zrewolucjonizować transport w regionie, a także wyznaczyć nowe standardy w budownictwie kolejowym w Polsce.